Advantages of Using Top Quality Abrasive Wheels
- Rebecca Rose
- Mar 24, 2022
- 3 min read
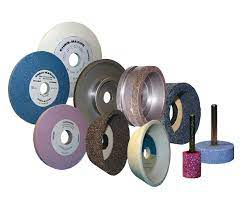
If you are a construction worker, you need top quality Abrasive Wheels for your project. These wheels are not only durable and efficient, but they also save you a great deal of time and effort. The quality of your finished product will improve, and you will enjoy the reduced amount of downtime and money you'll spend on wheel replacement. Here are some advantages of using abrasive wheels: They last a long time, which means your job will be easier and faster.
Selection of Abrasive Wheel
Firstly, the abrasive type you choose should match the work material. While there are a lot of different abrasive types, the selection is based on how they interact with the work material. The ideal abrasive will maintain sharp cutting points for a long time while dulling points will fracture to form new ones. There are many different abrasive materials available and the one you choose will depend on the purpose of your application.
The most common abrasive material used in cutting processes is aluminum oxide. It is used in carbon, alloy steel, bronze, and wrought iron. There are different styles of aluminum oxide abrasive, and they each perform well with different materials. Alumina is another type of abrasive material and is great for cut-off applications. These types of abrasive wheels have a specific density that can be used to maximize the cutting ability of your machine.
Size of Abrasive Wheels
Abrasive wheels come in a variety of sizes, with grain sizes ranging from ten (coarsest) to 600 grains. The coarser grains are used for fast cutting while the finer grains are used for finishing. The denser abrasive wheels have more space for coolant and can cut more deeply and wider with less coolant. However, the denser the abrasive, the greater the finish quality of the work.

The abrasive type is important when cutting steel or other materials. There are three basic types of abrasive: aluminum oxide, diamond, and silicon carbide. In addition to the abrasive's hardness, the abrasive's density has an impact on the cutting speed and surface finish. The denser abrasive has less space to work with, and the slower it cuts, the greater the surface finish will be.
Importance of Abrasive Wheels
Abrasive wheels are very important tools for cutting metal. The right abrasive wheel can help you achieve the desired results. When grinding metal, make sure that the abrasive wheel is made of the proper material for the job. Abrasive wheels are the best choice for this type of process. They can be purchased at a professional tool store or online. Abrasive wheel can help you achieve the results you need for your job.

Discs with diamonds are abrasive and are the best choice for hard metal grinding. They are durable and resistant to heat. Compared to diamond wheels, CBN wheels are more efficient. They are much more efficient in grinding. The abrasive discs can be used for a variety of applications, including cutting steel, rubber, and soft bronze. Abrasives are essential in a wide variety of industrial processes.
Durability and Performance
The durability and performance of abrasive wheels is determined by the bond between the abrasive and the resin. It is crucial to know that high-quality abrasive wheels are designed with safety in mind. In addition to the abrasive bond, the wheel's durability and performance depends on the materials it is made from. In addition to its durability, CBN wheels can withstand temperatures up to 1,000 degrees Celsius.
Abrasive wheels can be made from various materials. Some are made from plastic, while others are made from metal. The type of abrasive wheel that you need will depend on the material that you want to grind. For example, alumina is good for steel, while zirconia is better for zirconia. While diamond wheels can be used for non-metallic materials, they are suited for grinding steel and other metals.
Selection of Abrasive Wheels
When choosing abrasive wheels, make sure you know the grit that you need. Different abrasives are created for different types of materials. For instance, aluminum oxide is a popular abrasive for steel. While alumina and aluminum oxide are good for grinding aluminum, alumina is better for grinding carbon and bronze. They will reduce heat and produce a high-quality final product.
Comentários