The Many Uses of End Mills
- Rebecca Rose
- May 18, 2022
- 4 min read

You've probably seen advertisements for End Mills for cutting plastic and metal, but do you know how these tools work? These tools have a body shaped like a set of teeth, and their blades can cut materials into a variety of shapes and designs. If not, you can learn more about their uses below. There are many uses for End Mills, including making holes, grooves, slots, and grooving.
Shapes
The shapes of end mills depend on the project, material to be cut, and the desired surface finish. These factors help determine the right tooling for the task. Key tooling characteristics include diameter, shank, number of flutes, and tip shape. Each type of end mill has specific characteristics and is used for a specific purpose. Most common shapes include straight, ball nose, and fish-tail cutters. Straight end mills are suitable for flat or rounded surfaces, while bullnose and fish tail cutters are best for engraving.
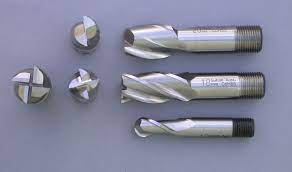
A semispherical end mill 22 has appropriate cutting teeth. This shape is defined by the convex bottom portion 32 and its perimeter or side 34. A sphere end mill, on the other hand, has an elongated shape. These two features are important for accurate machining, so they must be used together. The shape of the ball end mills depends on the application. A sphere end mill has a convex bottom portion.
Holes
An end mill is a tool used to cut holes in a variety of materials and for many different types of projects. Some end mills are more versatile than others and can take on a variety of features. If the features are routinely drilled, an end mill can save you time by eliminating the need to CAM or make chips. It is important, however, to remember that an end mill should not be blasted through the hole in one motion. Instead, it is advisable to program a quick retract after cutting a chip and letting coolant in.

Holes are another common use of end mills. Unlike drills, which need to run at very high speeds, end mills require a much slower speed and can evacuate chips more easily. End mills can be used to drill holes that have a flat bottom, and the depth of plunge is half or more of the diameter of the tool. Because of this, they can be used on thin materials such as wood or plastic.
Grooving
Grooving with End Mills can be performed using either a slotted or detachable cutter. Both types require special care when installing the cutters. Deep grooving requires special attention when installing the cutters. Even the tiniest error can result in friction between the groove walls and the cutter, resulting in breakage. Here are some steps that can help you achieve the best results with grooving with End Mills.

Before using end mills, machine shops had two main options for creating circular grooves on the face of a part. In the past, machine shops used static face grooving tools, which are not ideal for small parts. This is because they cannot be chucked in a turning center, and they cannot access bosses or out-of-balance conditions. Small-diameter end mills also have a high risk of tool breakage. Additionally, they usually produce symmetrical groove profiles.
Slots
End mills have several benefits. They are versatile, and their slanted design allows for multiple milling strategies. These end mills are particularly useful for shallow or closed slots. Despite their many advantages, end mills leave a rough finish on the material they cut. They are also not suited for cutting high-tensile strength or hard materials. Here are some tips to maximize the use of end mills.
Pre-finish grooving
Whether you are finishing blade root grooves, or pre-finish grooving a mold, there is an End Mill for the job. Milling cutters with a pine-tree shape are ideal for this task. With a helix angle of 30°, they produce fine finishing. The new concept geometry improves sharpness and the connection between the ball nose end cutting edge and the peripheral cutting edge. Thin web, unique flute geometry, and X-coat increase the abrasive wear resistance and feed rate.
Variable-helix-g-pitch End Mills are another option for pre-finish grooving. This design allows for varying distances between the cutting edge and the workpiece, which increases tool life and produces better results. These tools are ideal for deep slots and deep profiles and are also ideal for machining softer materials such as stainless steel. But they also work great for removing burrs and other contaminants.
Slot Drilling
Like end drills, slot drills are used to mill keyway slots on the faces and edges of materials. The difference between slot drills and end mills lies in the number of flutes, or cutting edges, that the tool has. This increases its ability to plunge into the material without breaking or clogging. They can also be made from a variety of materials, including carbide, powder metal, and HSS.
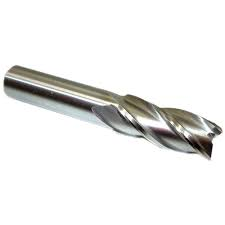
The center cutting edge of an end mill has a lower clearance than its side edges. This means that the chip removal is less than a drill with a side cutting edge. Typically, an end mill with a center cutting edge produces a good hole, but it can also produce a short peck. To prevent the need to change tools after the initial drilling, pre-drill the slot first. This will prevent the need for a tool change and minimize chip evacuation.
Comentarios