Why Wire Wrap Requires a Specialized Tool?
- Rebecca Rose
- May 19, 2022
- 4 min read
Updated: May 23, 2022
Wire wrapping provides a permanent electrical connection, which is superior to soldered connections. It also lends itself to automation but requires a rotating tool to be done properly. In this article, we will examine the various types of wire wrapping and how to determine which method is best for your application. In addition to the different types of wire wrap, you'll also learn why the method is so popular among electrical contractors and designers. Listed below are a few pros and cons of this technique.
Wire Wrapping is a Permanent Electrical Connection
The term "wire wrapping" describes the practice of securing wires together permanently, usually with a single wire. Wire wrapping was first used in the nineteenth century by telegraph linesmen, who needed to make connections between two wires in their central office. The process was eventually adapted for the telephone industry, which needed simpler connections at its central office. This development led to the creation of wire wrapping tools by Bell Labs and Western Electric.

Wire wrapping can be used in circuits with higher voltage and amperage than traditional methods. For example, a 12V 0.1A fan requires a wire thick enough to withstand its current. To determine what diameter is required, look at an AWG chart. The thinner the wire, the higher the risk of electrical shock to the human body. For larger wires, use a multi-conductor connector.
It is More Reliable than Soldered Connections
Compared to soldered connections, Wire Wrap is more reliable because the single turn of the wire makes four contacts to the post on each corner. The process also uses a tool that applies tons of force per square inch, which almost cold welds the wire to the post. A properly made wire wrap connection will have 0.5 to 1.5 turns of insulated wire at the bottom and six to seven turns of stripped silver-plated wire around the post. This method produces 24 to 28 airtight connections.
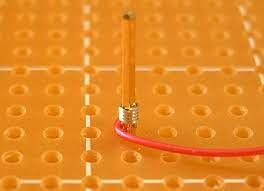
While both crimping and soldering methods can produce solid mechanical connections, some technicians prefer a combination of the two. With soldering, the contact first is crimped, and the solder follows. The result is a secure connection that never fails. With solder, the connection is not as strong as a wire wrap because it lacks compression strength. Also, the soldering process requires the cable to be stripped properly. Stripping must be done at 90 degrees.
It Lends Itself to Automation
Among the many manufacturing techniques used in computer engineering, Wire Wrap lends itself to automation. While wire wrapping is a time-honored method, it is also remarkably flexible. The wire-wrapping process can easily assemble twisted pairs, twisted magnetic shielded quads, and even high-speed digital circuits. It is an ideal choice for production runs requiring precise control over wire length and a high degree of automation.
It Requires a Rotating Tool
To begin Wire Wrap, you must have a specialized tool. The tool is called a "bit" and has a large hole in its face that marks the rotation point on the terminal. The shaped contour of the bit helps guide the wire into a tight helix. The wire is then held in place by a sleeve. This sleeve also protects the worker from abrasions while keeping the wire in place.

When first starting, wire wrap tools can have sharp edges. Attempting to wrap a wire without using the correct bit will result in a pigtail or loose wrap. You will need to select the right wire gauge, insulation, and terminal diagonal for the job. Once you have chosen the right tools, you will be able to complete wire wrapping without any issues. If you have any doubts, ask a knowledgeable electrician for help.
It Requires a Minimum Number of Complete Turns
Before completing a wire-wrapping process, you should first know how many complete turns you need for a good wrap. A good wrap has at least three turns of exposed wire and at least one turn of insulated wire wrapped around the post. Regardless of the type of termination, the first turn must be close to the ground and the remaining turns should be snugly wrapped around the post. Typically, a wire-wrapping process requires seven full turns of exposed wire to protect the post from the elements. The minimum number of turns is determined by a wire's function and MIL-STD-1130B or engineering documentation.
The length of each turn must be at least one / four inches. The wire ends must be at least one / 64" away from the previous connection. Then, solder them together using the proper wire wrap tool. The correct number of complete turns will depend on the size of the terminal and the length of the wire. For example, a 6-turn wire wrap requires one / 4" of terminal length.
It is Popular in Telecommunications
Wire wrapping has its roots in the suburbs of New Jersey, where the practice first began with telegraph linesmen. Later, the telephone industry needed better connections between equipment in its central office, and wire wrapping was developed. Western Electric and Bell Labs both developed wire wrapping tools and manufactured wire wrap products. Today, wire wrap is used to connect wires to make a clean metal-to-metal electrical connection.

The basic wire wrap technique consists of wrapping uninsulated copper wire around a terminal. This method is a popular choice for cross-connections between different devices. A wire wrap gun looks like a drill and fits over a terminal, feeding the wire through it. Wire wrap guns are a fast and reliable way to wrap wires and are very precise. The wire wrap gun is calibrated to the thickness of the copper wire, which makes it automatically twist and flow around the terminal with the appropriate strength and frequency.
Comments